How to calculate the cost of goods sold to make a profit – With the secrets of COGS (Cost of Goods Sold) unlocked, we embark on a captivating journey to decipher its intricacies and unravel its power in driving profitability. Join us as we delve into the depths of this financial metric, uncovering the strategies and insights that will transform your understanding of cost optimization and maximize your profit margins.
In this comprehensive guide, we’ll explore the components of COGS, unravel the art of calculating direct material and labor costs, and shed light on the allocation of manufacturing overhead. We’ll also navigate the complexities of inventory valuation, discounts, and allowances, empowering you with the knowledge to make informed decisions that fuel your business growth.
Definition of Cost of Goods Sold (COGS)
Cost of Goods Sold (COGS) is the direct cost incurred by a company to produce the goods it sells. It includes the cost of raw materials, direct labor, and manufacturing overhead.
COGS is a key factor in determining a company’s profitability. A company’s gross profit is calculated by subtracting COGS from its revenue. Gross profit is then used to calculate a company’s net profit, which is its profit after all expenses have been paid.
Components of COGS
The following are the main components of COGS:
- Raw materials:The cost of the materials used to make the product.
- Direct labor:The cost of the labor directly involved in producing the product.
- Manufacturing overhead:The cost of indirect expenses incurred in the production process, such as rent, utilities, and depreciation.
Calculating Direct Material Costs
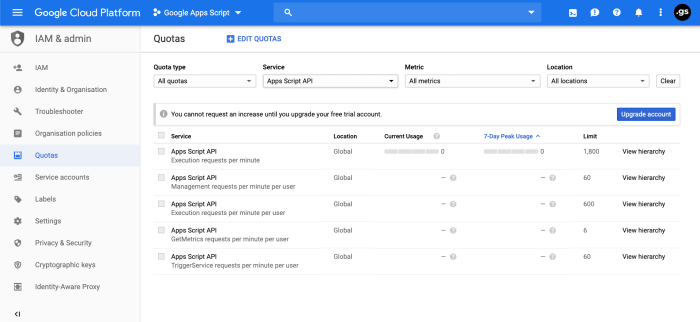
Calculating direct material costs is crucial for determining the Cost of Goods Sold (COGS) and ensuring accurate financial reporting. Here are the common methods used:
- First-In, First-Out (FIFO):Assumes that the first materials purchased are the first ones used in production, so the cost of goods sold is based on the oldest inventory costs.
- Last-In, First-Out (LIFO):Assumes that the most recently purchased materials are the first ones used in production, so the cost of goods sold is based on the most recent inventory costs.
- Weighted Average Cost:Calculates the average cost of all materials available for use during a period, regardless of when they were purchased. This method provides a more stable cost of goods sold over time.
Importance of Inventory Management:Accurate inventory management is essential for calculating direct material costs. It ensures that the company has a clear understanding of the quantity and cost of materials on hand, which is crucial for determining the cost of goods sold and managing production efficiently.
Calculating Direct Labor Costs: How To Calculate The Cost Of Goods Sold To Make A Profit
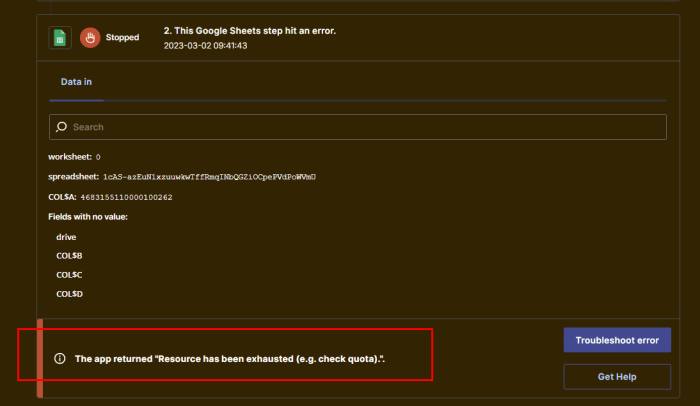
Direct labor costs represent the wages paid to employees directly involved in the production of goods. These costs are calculated based on the number of hours worked and the hourly wage rate.
Formula for Calculating Direct Labor Costs
The formula for calculating direct labor costs is:
Direct Labor Costs = Number of Hours Worked x Hourly Wage Rate
For example, if a production worker works 40 hours per week and earns $15 per hour, the direct labor cost for that week would be:
Direct Labor Costs = 40 hours x $15/hour = $600
Factors Influencing Labor Costs
Several factors can influence labor costs, including:
- Minimum wage laws:Minimum wage laws set the lowest legal hourly wage that employers can pay their employees.
- Union contracts:Union contracts often negotiate higher wages and benefits for unionized workers.
- Industry and job type:Different industries and job types have varying wage scales.
- Experience and skill level:Employees with more experience and higher skill levels typically earn higher wages.
- Location:The cost of living in different locations can impact wage rates.
Calculating Manufacturing Overhead Costs
Manufacturing overhead costs (MOH) are indirect costs associated with the production process but not directly related to the production of a specific unit of product. They include costs like factory rent, utilities, and depreciation of equipment. Accurate allocation of MOH is crucial for determining the cost of goods sold (COGS) and profitability.
To determine your profit margin, it’s crucial to accurately calculate the cost of goods sold. This involves factoring in direct and indirect costs associated with production. Enhance your financial literacy with Learn Solidity: A Comprehensive Guide to Web Development with Solidity , a valuable resource for understanding complex financial concepts.
By mastering cost of goods sold calculations, you’ll gain a competitive edge in managing your business and maximizing profitability.
There are various types of MOH:
- Indirect materials: Consumables not directly used in the product, like lubricants or cleaning supplies.
- Indirect labor: Salaries and wages of non-production personnel, such as supervisors or maintenance staff.
- Utilities: Costs of electricity, water, and gas used in the factory.
- Depreciation: Reduction in the value of factory assets, like machinery or buildings, over time.
- Rent: Cost of leasing or owning the factory space.
To allocate MOH, businesses use different methods, including:
- Activity-based costing (ABC): Assigns costs based on the activities that consume resources.
- Plant-wide overhead rate: Distributes costs based on a single overhead rate for the entire factory.
- Departmental overhead rate: Divides costs among different departments within the factory.
The choice of allocation method depends on factors such as the size and complexity of the factory, the number of products produced, and the availability of data.
Estimating Production Volume
Estimating production volume is a crucial step in calculating COGS, as it directly affects the quantity of materials, labor, and overhead costs incurred.
Various techniques can be used for production volume estimation, including:
- Historical Data:Analyzing past production records and trends to project future volume.
- Market Research:Conducting surveys, focus groups, or market analysis to estimate demand for the product.
- Industry Benchmarks:Comparing the company’s production capacity and efficiency to industry averages.
- Sales Forecasts:Using sales projections and customer orders to estimate the required production volume.
- Capacity Planning:Assessing the company’s production capabilities and identifying potential bottlenecks to determine the maximum feasible production volume.
Impact of Production Volume on COGS
Production volume significantly impacts COGS:
- Fixed Costs:Fixed costs (e.g., rent, salaries) remain constant regardless of production volume.
- Variable Costs:Variable costs (e.g., materials, direct labor) increase or decrease proportionally with production volume.
- Unit Cost:The unit cost of goods produced (COGS divided by production volume) decreases as production volume increases, due to the spreading of fixed costs over a larger number of units.
- Profitability:Higher production volume generally leads to lower unit costs and higher profit margins.
Cost Allocation and Markups
To calculate the cost of goods sold (COGS) accurately, businesses must allocate costs to their products and determine appropriate markups. This ensures that the COGS reflects the actual costs incurred in producing the goods and allows for a reasonable profit margin.
There are various methods for allocating costs to products, including:
- Direct Costing:Assigns only direct material and direct labor costs to products.
- Absorption Costing:Allocates both direct and indirect manufacturing costs to products.
- Activity-Based Costing (ABC):Assigns costs based on the activities required to produce the products.
The choice of cost allocation method depends on the industry, product characteristics, and available data.
Determining Appropriate Markups
Once costs have been allocated to products, businesses need to determine appropriate markups to ensure profitability. Markups are a percentage added to the COGS to cover indirect costs and generate a profit.
Factors to consider when determining markups include:
- Industry standards and competition
- Target profit margin
- Market demand and elasticity
- Cost of goods sold
Businesses can use markup formulas to calculate the markup percentage based on these factors. By carefully allocating costs and determining appropriate markups, businesses can ensure accurate COGS calculations and achieve desired profit margins.
Inventory Valuation Methods

Inventory valuation methods play a crucial role in determining the cost of goods sold (COGS). Different methods result in varying COGS amounts, which can impact a company’s profitability and financial statements.
Specific Inventory Valuation Methods
There are several commonly used inventory valuation methods, each with its own advantages and disadvantages:
-
-*First-In, First-Out (FIFO)
This method assumes that the oldest inventory items are sold first. The cost of goods sold is based on the cost of the earliest purchases. FIFO tends to result in a higher COGS during periods of rising prices.
-*Last-In, First-Out (LIFO)
This method assumes that the most recently purchased inventory items are sold first. The cost of goods sold is based on the cost of the latest purchases. LIFO tends to result in a lower COGS during periods of rising prices.
-*Weighted Average Cost
Calculating the cost of goods sold is essential for determining profitability. Understanding how to do so is crucial for businesses of all sizes. One resource that can assist in this endeavor is Smart Contracts with Solidity: A Comprehensive Guide to Blockchain Development . This guide provides valuable insights into the world of blockchain technology and its applications.
By leveraging this knowledge, businesses can streamline their operations and optimize their profitability through accurate cost of goods sold calculations.
This method calculates the average cost of all inventory items available for sale during a period. The cost of goods sold is based on this average cost. Weighted average cost tends to result in a more stable COGS over time.
-*Specific Identification
This method assigns a specific cost to each inventory item. The cost of goods sold is based on the cost of the specific items sold. Specific identification is often used for high-value or unique inventory items.
The choice of inventory valuation method can have a significant impact on a company’s financial statements. It is important for companies to carefully consider the different methods and select the one that best suits their specific circumstances.
Accounting for Discounts and Allowances

Discounts and allowances are reductions in the price of goods sold. They can be offered to customers for a variety of reasons, such as to promote sales, reward loyalty, or clear out excess inventory.
When discounts and allowances are offered, they must be accounted for in the calculation of COGS. This is because discounts and allowances reduce the amount of revenue that is recognized from the sale of goods. As a result, they also reduce the amount of gross profit that is earned.
Common Discounts and Allowances
There are many different types of discounts and allowances that can be offered to customers. Some of the most common include:
- Trade discountsare discounts that are offered to businesses that purchase large quantities of goods.
- Quantity discountsare discounts that are offered to customers who purchase a certain number of items.
- Seasonal discountsare discounts that are offered during certain times of the year, such as during holidays or clearance sales.
- Cash discountsare discounts that are offered to customers who pay for their purchases in cash.
- Allowancesare reductions in the price of goods that are made for reasons such as damaged goods or incorrect shipments.
Using COGS to Determine Profitability
Cost of Goods Sold (COGS) plays a crucial role in determining a company’s profitability. It directly impacts profit margins and provides valuable insights into a company’s efficiency and cost management.
Profitability refers to a company’s ability to generate profits from its operations. It is typically measured by calculating profit margins, which represent the percentage of profit earned for each unit of revenue.
To determine the profit margin, it’s crucial to calculate the cost of goods sold accurately. Understanding this concept can help you make informed decisions about pricing and inventory management. If you’re looking to expand your business into the digital realm, consider exploring How to Build a Web3 NFT Minting Platform: A Comprehensive Guide . This resource provides valuable insights into creating an NFT minting platform, empowering you to capitalize on the growing Web3 ecosystem.
By calculating the cost of goods sold, you can optimize your operations and maximize profitability in both traditional and digital ventures.
Gross Profit Margin
Gross profit margin measures the profitability of a company’s core business operations. It is calculated by dividing gross profit (revenue minus COGS) by revenue.
Gross Profit Margin = (Revenue
COGS) / Revenue
A higher gross profit margin indicates that a company is effectively managing its COGS and generating a significant portion of revenue as profit.
Operating Profit Margin
Operating profit margin considers a broader range of expenses, including selling, general, and administrative (SG&A) expenses. It is calculated by dividing operating profit (gross profit minus SG&A expenses) by revenue.
Understanding how to calculate the cost of goods sold is crucial for maximizing profits. Whether you’re a seasoned entrepreneur or an aspiring NFT creator, mastering this concept is essential. Explore Sell NFTs Online: A Comprehensive Guide for Success to delve into the world of digital art and discover strategies for selling your creations.
With a clear understanding of COGS, you can optimize your pricing and ensure profitability in both traditional and online ventures.
Operating Profit Margin = (Gross Profit
Calculating the cost of goods sold is crucial for maximizing profits. Just like the fluctuating value of NFT or Coin: Unraveling the Enigma of Digital Assets , understanding the costs associated with producing and selling your products is essential. Accurately calculating these costs will help you set appropriate prices, make informed decisions, and ultimately boost your profitability.
SG&A Expenses) / Revenue
A higher operating profit margin suggests that a company is efficiently controlling its overall operating costs and generating a sustainable level of profit.
Net Profit Margin, How to calculate the cost of goods sold to make a profit
Net profit margin represents the ultimate profitability of a company. It is calculated by dividing net income (revenue minus all expenses, including COGS, SG&A, and other non-operating expenses) by revenue.
Net Profit Margin = Net Income / Revenue
A higher net profit margin indicates that a company is effectively managing its expenses and generating a substantial portion of revenue as net profit.
Final Wrap-Up
Mastering the calculation of COGS is not merely an accounting exercise; it’s a transformative skill that empowers businesses to optimize their operations, minimize expenses, and maximize profitability. By embracing the insights shared in this guide, you’ll gain the competitive edge necessary to navigate market fluctuations, increase your profit margins, and achieve sustainable financial success.
FAQ Section
What exactly is COGS?
COGS (Cost of Goods Sold) represents the direct costs associated with producing the goods sold by a business. It includes the costs of raw materials, direct labor, and manufacturing overhead.
How do I calculate direct material costs?
Direct material costs can be calculated using various methods, including the weighted average method, FIFO (First-In, First-Out) method, and LIFO (Last-In, First-Out) method.
What factors influence labor costs?
Labor costs are influenced by factors such as wage rates, employee benefits, overtime pay, and payroll taxes.
How do I allocate manufacturing overhead costs?
Manufacturing overhead costs can be allocated using methods such as the activity-based costing method or the absorption costing method.
What is the impact of inventory valuation on COGS?
The choice of inventory valuation method, such as FIFO or LIFO, can impact the COGS calculation and affect the reported profitability of a business.